The demand for metal laser cutting continues to grow as industries look for precise, efficient, and cost-effective ways to fabricate metal parts and components. Whether you’re in the automotive, aerospace, construction, or manufacturing sector, having access to a reliable metal laser cutter supplier is essential for maintaining high-quality standards and meeting production deadlines.
Advantages of Laser Cutting Technology
Laser cutting isn’t just another fabrication method—it’s a game-changer. Embracing this technology unlocks a world of precision, efficiency, and versatility.
High Precision and Accuracy
Laser cutters slice through materials with pinpoint accuracy, down to fractions of a millimeter. Imagine crafting components that fit together like pieces of a puzzle—no gaps, no errors. That’s the power of laser precision.
The laser beam’s focused heat ensures minimal distortion, so your metal retains its integrity. Forget about the rough edges and imperfections of traditional cutting methods. With laser cutting, you get clean, smooth edges every time.
Capability for Complex Designs
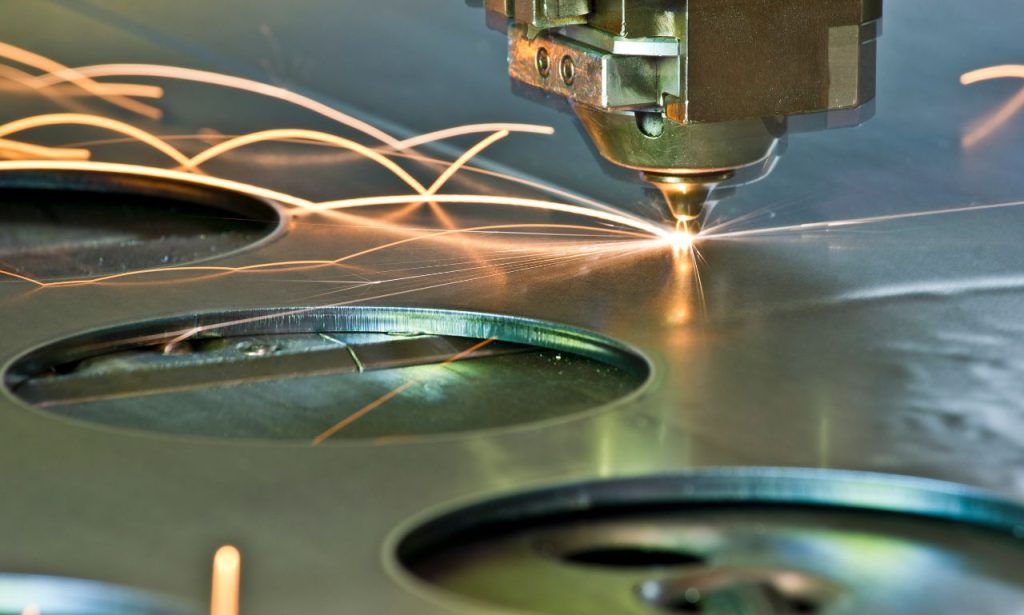
Ever dreamt of bringing intricate designs to life? Laser cutting turns those dreams into reality. Whether it’s delicate filigree patterns or complex geometric shapes, lasers handle them with ease.
Traditional cutting tools might falter when faced with complex designs. Not lasers. They follow your design specifications to the letter, carving out even the most elaborate details with finesse. This opens up endless possibilities for creativity and innovation in metal fabrication.
Versatility in Material Processing
Laser cutters aren’t picky—they handle a wide range of metals, from stainless steel to aluminum, brass to copper. Whether you’re working with thin sheets or hefty plates, lasers adapt to your material needs.
This versatility means you don’t need multiple machines for different materials. One laser cutter, countless possibilities. It’s efficiency and flexibility rolled into one powerful package.
Key Considerations in Metal Fabrication
Before getting into metal fabrication, there are crucial factors to keep in mind which can save you time, money, and a whole lot of headaches.
Understanding Different Metal Types
Each type brings its own set of properties—strength, malleability, conductivity—that affect how it should be cut and used.
For instance, stainless steel is tough and corrosion-resistant, making it great for durable applications. Aluminum is lightweight and versatile, perfect for projects where weight is a concern. Knowing your metals helps you choose the right one for your project and ensures optimal results from your laser cutting process.
Material Thickness and Compatibility
The thickness of your metal affects the laser cutter’s performance and the quality of the cut. Lasers have limits on how thick they can cut effectively.
Choosing a metal laser cutter supplier who understands material compatibility is key. They can advise on the best settings and equipment for your material’s thickness, ensuring clean cuts without compromising the metal’s integrity.
Project Requirements and Specifications
From the design challenges to the final application, understanding your project’s specific needs is crucial. Are tight tolerances required? Is there a need for specific finishes? Knowing these details guides the fabrication process.
Communicate your requirements clearly with your supplier. A good metal laser cutter supplier will work with you to meet your specifications, delivering a product that fits your vision like a glove.
Types of Laser Cutters
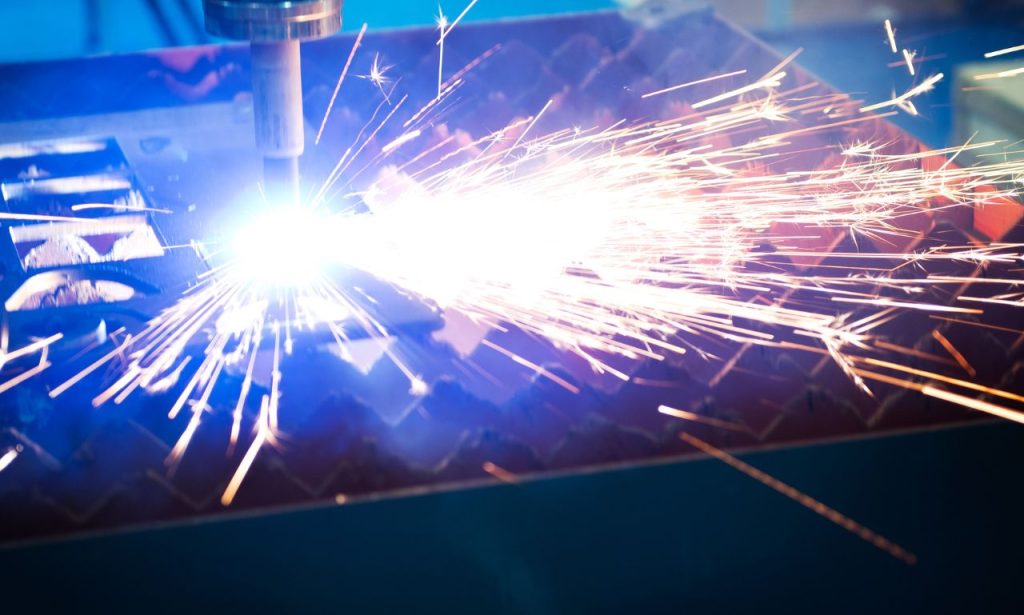
Not all laser cutters are the same. Different types harness various technologies and offer distinct advantages. Let’s break down the main types you might encounter.
CO2 Laser Cutters
CO2 lasers are veterans in laser cutting. Using a gas mixture excited by electrical energy, they produce a powerful infrared laser beam.
These cutters are excellent for non-metal materials like wood and acrylic but are also capable of cutting certain metals. They offer smooth cuts and are relatively cost-effective. If versatility across materials is a priority, CO2 lasers are a solid choice.
Fiber Laser Cutters
Fiber lasers are the new kids on the block, and they’re making a splash. They use optical fibers doped with rare earth elements to generate a laser beam.
Fiber lasers are incredibly efficient, with high power outputs suitable for cutting various metals, including reflective ones like aluminum and copper. They offer faster cutting speeds and lower maintenance than CO2 lasers. If you’re focusing on metal cutting, fiber lasers are the way to go.
Nd:YAG Laser Cutters
Neodymium-doped Yttrium Aluminum Garnet (Nd:YAG) lasers might be a mouthful, but they’re worth knowing. These solid-state lasers produce a highly concentrated beam capable of cutting and engraving.
They’re excellent for applications requiring high power over a small area, like deep welding or cutting thick metals. While not as common as CO2 or fiber lasers, Nd:YAG lasers fill a niche for specific industrial applications.
The Laser Cutting Process
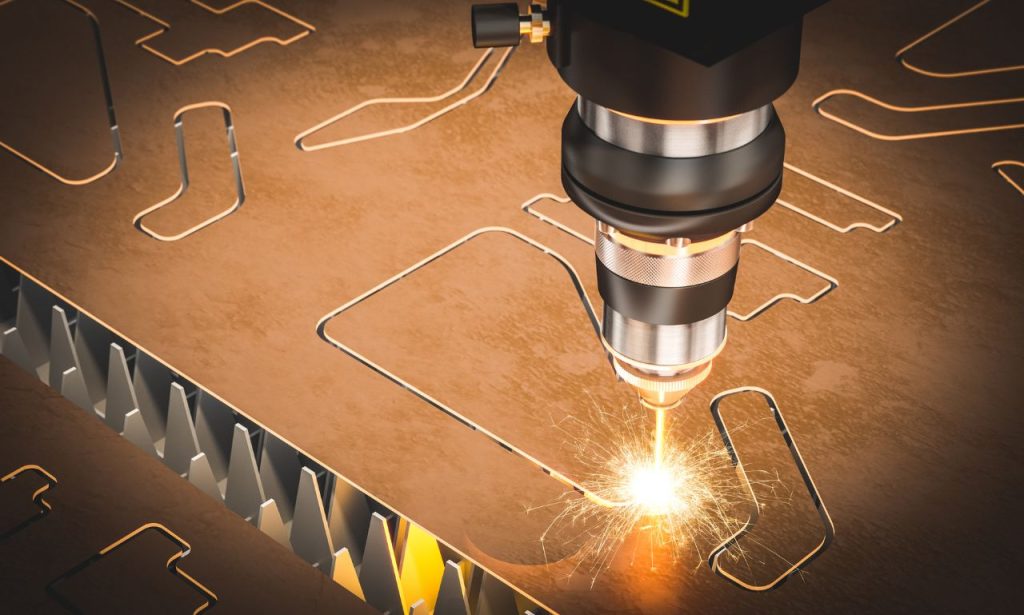
Understanding the laser cutting process demystifies the technology and helps you appreciate its capabilities. Let’s walk through the key stages.
Preparation and Setup
Before the laser ever fires up, preparation is key. It starts with designing your project using CAD software. Precision in this stage ensures the laser follows the exact path you intend.
Next comes material selection and placement. Ensuring the metal is clean and properly secured on the cutting bed prevents errors. The laser’s settings—power, speed, focus—are adjusted based on the material type and thickness.
The Cutting Operation
Once setup is complete, it’s showtime. The laser cutter directs the focused beam onto the metal, heating and melting it precisely along the designated path.
Assist gases like oxygen or nitrogen may be used to blow away molten material, improving cut quality and speed. The laser moves—or in some cases, the material moves—guided by the programmed design. The result? Precise cuts that bring your design to life.
Post-Processing Requirements
After cutting, some parts may require post-processing. This could include deburring edges, cleaning the metal, or applying finishes.
Laser cutting often minimizes the need for extensive post-processing due to its precision and clean cuts. However, depending on the project’s requirements, a few finishing touches might be necessary to achieve the perfect end product.
Safety Measures in Laser Cutting
Safety isn’t optional—it’s essential. High-powered lasers demand respect and adherence to safety protocols to protect both operators and equipment.
Equipment Safety Protocols
Laser cutters are sophisticated machines with moving parts and high voltages. Regular maintenance and inspections keep them running safely and efficiently.
Protective enclosures and interlocks prevent accidental exposure to the laser beam. Emergency stop buttons should be accessible, and all operators must be trained in shutdown procedures in case something goes awry.
Personal Protective Equipment (PPE)
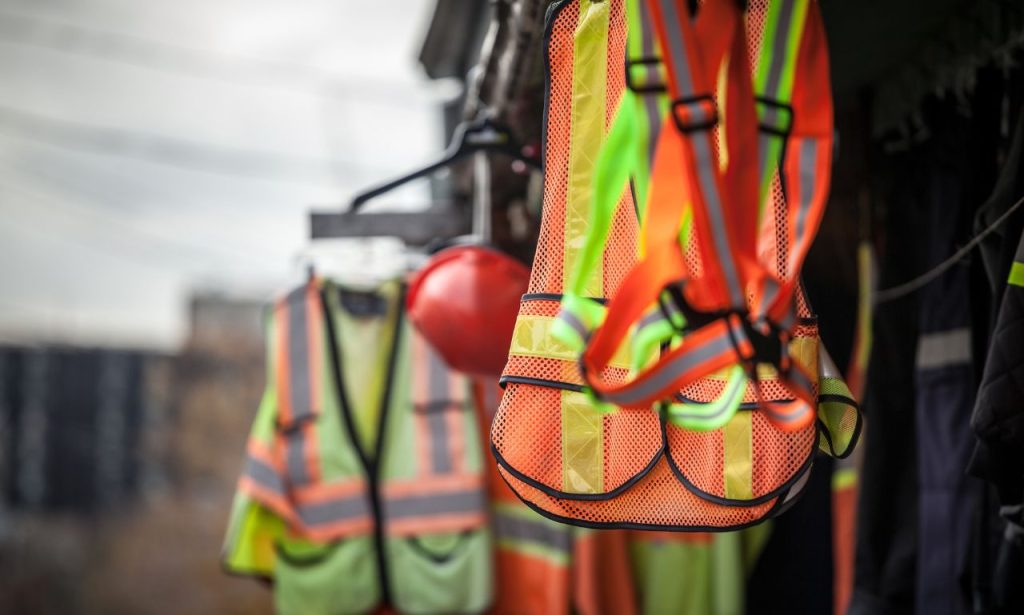
Operators need to gear up appropriately. Safety goggles designed for the specific laser wavelength protect eyes from stray beams. Fire-resistant clothing shields against sparks and heat.
Gloves and safety boots add another layer of protection. Remember, PPE is your last line of defense—it shouldn’t replace safe operating procedures but rather complement them.
Workplace Safety Practices
Creating a culture of safety in the workplace pays dividends. Keep the laser cutting area clean and free of flammable materials. Implement proper ventilation to remove fumes and gases generated during cutting.
Training is paramount. Ensure everyone involved understands the risks and the correct procedures. A well-informed team is a safer team.
Evaluating Suppliers
Choosing the right metal laser cutter suppliers isn’t just about who offers the lowest price. It’s about finding a partner who meets your needs and supports your goals.
Assessing Machine Capabilities
Not all suppliers have the same equipment. Evaluate their laser cutters—do they have the type and power suitable for your projects? Can they handle the materials and thicknesses you require?
Ask about their technology—are they using the latest fiber lasers, or are they relying on older models? Advanced machines often mean better precision and efficiency.
Reviewing Customer Service and Support
Good suppliers offer more than just equipment—they provide support. Assess their customer service responsiveness. Do they answer your questions promptly? Are they willing to provide references or case studies?
Consider their willingness to collaborate. A supplier who understands your vision and works with you to achieve it is invaluable.
Cost Considerations and Budgeting
Budget matters, but it’s not the only factor. Analyze the cost in relation to the value offered. A cheaper supplier might save you money upfront but could cost more in the long run if quality suffers.
Look for transparent pricing without hidden fees. Understand what’s included—are setup, maintenance, or post-processing extra? Make informed decisions based on the full picture.
Making Informed Decisions
Choosing a supplier is a significant decision. It’s about more than just a transaction; it’s about building a partnership that propels your business forward.
Aligning Supplier Offerings with Business Needs
Your supplier should be a good fit for your business. If you’re producing high-volume orders, can they handle the scale? If you require specialized materials or intricate designs, do they have the expertise?
Assess how their capabilities align with your current needs and future plans. A supplier who can grow with you is a valuable asset.
Long-Term Maintenance and Support
Equipment needs upkeep. Ensure your supplier offers maintenance and support services. Downtime due to equipment failure can be costly.
Ask about their service agreements—do they offer regular maintenance checks? What’s their response time for repairs? Reliable support keeps your operations running smoothly.
Building a Relationship with Suppliers
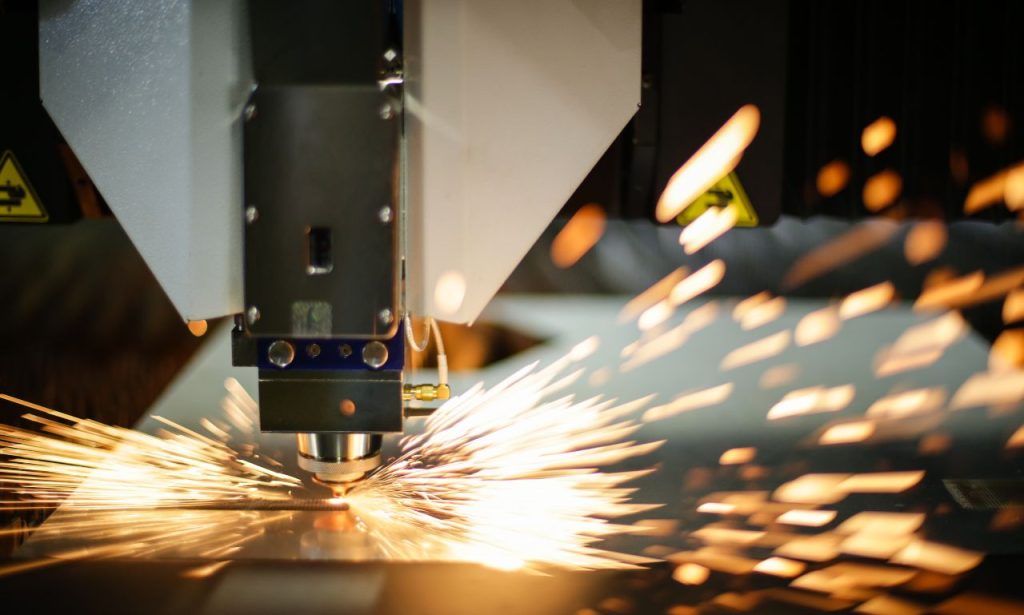
At the end of the day, it’s about relationships. Open communication fosters trust and leads to better outcomes. Don’t hesitate to share your goals and challenges.
A supplier who understands your business becomes a partner in your success. Together, you can push the boundaries of what’s possible in metal fabrication.
Ready to take your projects to the next level? Partner with expert metal laser cutter suppliers and watch your visions come to life with precision and style.
ALSO READ: Why CNC Machining Services in Italy Are The Key to Quality Parts
FAQs
A: Consider the materials you’re working with and the precision required. Fiber lasers excel at cutting various metals with high speed and accuracy. If you’re dealing with reflective metals like aluminum or copper, fiber lasers are particularly effective.
A: Absolutely! Laser cutting is ideal for prototyping due to its precision and ability to handle complex designs. It allows for rapid iteration, so you can refine your designs without significant delays.
A: Several factors influence cost, including material type and thickness, complexity of the design, volume of the order, and any additional post-processing requirements. Discussing your project details with suppliers can help you get an accurate quote.
A: Laser cutting is often more sustainable as it produces less waste due to its precision. Additionally, modern laser cutters are energy-efficient, and some suppliers offer eco-friendly options like recycling scrap materials.